Hydraulic Reciprocating Fiberglass Pultrusion Equipment, used in conjunction with fiberglass pultrusion molds, is primarily designed for the pultrusion of various fiberglass profiles. This fiberglass pultrusion equipment boasts high production efficiency, stable product quality, and ease of operation. The production process generates no scrap material, saving labor, raw materials, and energy consumption.
Main Applications The fiberglass pultrusion production line is mainly used for producing various fiberglass pultrusion profiles, such as fiberglass panels, fiberglass square tubes, fiberglass square rods, fiberglass angle profiles, and fiberglass channel profiles.
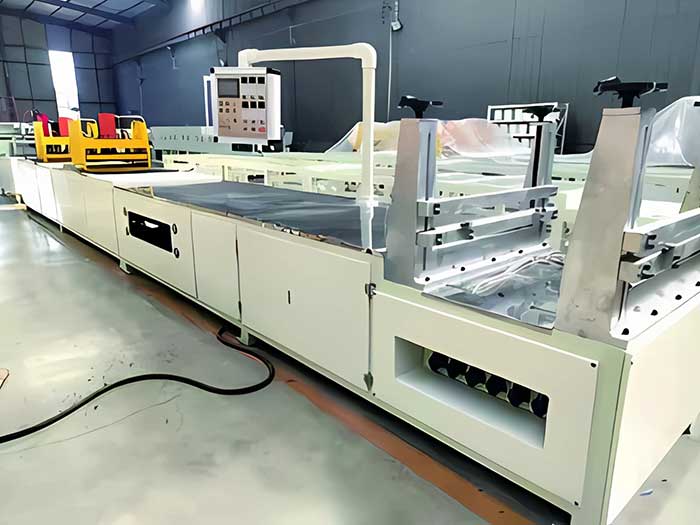
Main Components Fiberglass pultrusion production equipment typically comprises the following main parts:
- Creel: Used for placing glass fiber rovings or other continuous reinforcement materials.
- Resin Bath: Impregnates the fiber material with resin, ensuring uniform coverage.
- Pre-forming Table: Performs preliminary forming of the impregnated material.
- Puller: Uses mechanical, hydraulic, or electric drive to pull the formed material to achieve the desired shape and size.
- Cutting Saw: Cuts the formed material to ensure that the length and shape meet the requirements.
- Stacking Rack: Places finished products for subsequent handling and packaging.
- Control System: Typically uses a PLC control system, combined with a touchscreen, servo motors, and other equipment to achieve automated operation.
Main Technical Parameters
- Production line center height: 1000mm
- Maximum pulling width: 1000mm
- Cutting end face dimensions: 700×200mm
- Total power (excluding mold heating power): 12kW
- Pulling force: 300KN
- Overall dimensions of the production line: Length 26000×Width 1200×Height 1900mm
Features of the Fiberglass Pultrusion Production Line
- Mold Heating Control: Uses an intelligent temperature controller for automatic temperature control, with multi-point temperature measurement (3 zones, 6 points) for more precise mold temperature control.
- Puller: Adopts hydraulic reciprocating alternate pulling. The hydraulic system uses low-pressure large cylinders to ensure large pulling force, smooth pulling speed, and low system load, thereby extending the service life of hydraulic components.
- Hydraulic Systems: Two hydraulic systems control two pulling frames respectively, using precision speed control valves for speed regulation, making operation simple and convenient.
- Adjustable Pressure: System pressure and clamping pressure are adjustable to ensure sufficient pressure for product production without damaging the products.
- Cooling System: Equipped with a large-area cooler with water circulation to cool the system oil temperature. The system includes a circulating water tank and pipeline pump for customer convenience.
- Control System: The entire production line uses PLC programming control and can also be operated directly with buttons. It features pause and slow-motion functions for easy and simple operation.